Dispensing Booth - Pharmaceutical Weighing Booth
I. What is a Pharmaceutical Dispensing Booth?
A Dispensing Booth is a specialized cleanroom device used in pharmaceutical plants to control dust contamination and ensure safety during the weighing and dispensing of active ingredients. It protects operators, products, and the environment from cross-contamination while complying with GMP and ISO 14644 standards.

II. Why Does a Dispensing Booth in Pharmaceuticals Use Negative Pressure?
In pharmaceuticals, Dispensing Booths typically employ negative pressure to prevent dust and hazardous chemicals from escaping, safeguarding the surrounding environment and operator health. Key reasons include:
- Cross-contamination control: Negative pressure traps fine dust and API particles inside the booth, preventing spread to the cleanroom.
- Operator safety: Protects against inhalation of harmful APIs by containing particles and filtering exhaust air.
- GMP and ISO 14644 compliance: Ensures a safe production environment, minimizing contamination risks.
- Hazard containment: Prevents toxic particles from escaping during high-risk weighing or dispensing.
III. Operating Principle of a Dispensing Booth
- Clean air (HEPA-filtered) enters from the ventilation chamber (ceiling).
- A "downward airflow" carries dust particles away.
- "Dirty" air is drawn into the lower ventilation chamber (rear wall).
- Contaminated air is filtered (pre-filter and HEPA) and typically recirculated.
- Provides a unidirectional airflow from the ceiling at 0.45-0.5 m/s, measured ~1 m from the ceiling.
- Average air velocity per exhaust panel varies by no more than 10% from the overall average, with no point deviating over 5% from the panel’s mean (measured 25 mm from the grille).
- As the booth lacks one wall, external air enters; ~10% of air escapes via exhaust, maintaining a vacuum inside despite pressurization efforts.
IV. Technical Specifications of a Dispensing Booth
- Cleanliness level: ISO Class 5-7.
- Airflow velocity: 0.3-0.5 m/s.
- HEPA filter: 99.995% efficiency at 0.3 microns.
- Noise level: <65 dB.
- Power supply: 220V/50Hz or 380V/60Hz.
- Material: SUS 304/316L stainless steel or powder-coated steel.
- Control system: Touchscreen, pressure sensors, safety alerts.
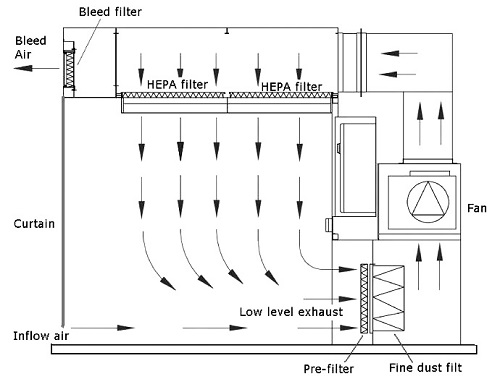
V. Key Features of a Dispensing Booth
- 3-stage filtration: Pre-filter, intermediate, and HEPA/ULPA for optimal air quality.
- Double-wall design: Enhances durability and airflow control.
- Gel-sealed HEPA filter: Superior to gasket filters in efficiency.
- Anti-glare LED lighting: Reduces eye strain, optimizes workspace.
- Removable exhaust grilles: Easy cleaning and maintenance.
- Smart monitoring: Pressure sensors and error alerts ensure performance.
VI. Applications of a Dispensing Booth
- Weighing and dispensing powders: Handling materials for tablets and powders.
- API sampling: Managing toxic pharmaceutical ingredients.
- Pharmaceutical compounding: Ensuring a clean lab or plant environment.
- GMP compliance: Meeting international pharmaceutical standards.
VII. Benefits of Using a Dispensing Booth
- Protects operator health from dust and toxic chemicals.
- Maintains GMP and ISO 14644 standards in production.
- Extends equipment and filter lifespan with optimized airflow control.
- Reduces cross-contamination risks during material handling.
VIII. Contact Us
BACH LONG PRODUCTION TRADING SERVICE CO., LTD
- Address: 75 Nguyen Hong Street, Ward 1, Go Vap District, Ho Chi Minh City, Vietnam
- Hotline: +84 93 143 54 54
- Email: sales@congnghelockhi.vn
- Website: www.congnghelockhi.vn
Dispensing Booth is an optimal solution for contamination control, ensuring safe and compliant pharmaceutical production. Contact us for design, sizing, or customization advice today!